The world of 3D printing is constantly evolving, with new technologies and applications emerging at a rapid pace. Among the various 3D printing methods, Selective Laser Sintering (SLS) stands out as a powerful and versatile technique, playing a crucial role in revolutionizing diverse industries. This article delves into the intricate workings of SLS, exploring its strengths, limitations, applications, and future potential.
Introduction
In recent years, the manufacturing industry has witnessed a significant transformation with the widespread adoption of 3D printing. This technology has not only simplified the production process but has also opened up new possibilities for creating complex and customized products. Of all the 3D printing techniques, Selective Laser Sintering (SLS) has emerged as a game-changer, offering unmatched flexibility, speed, and precision in manufacturing. SLS has been successfully implemented in various industries, including aerospace, automotive, healthcare, and consumer products, making it one of the most sought-after additive manufacturing processes.
Overview of Selective Laser Sintering (SLS)
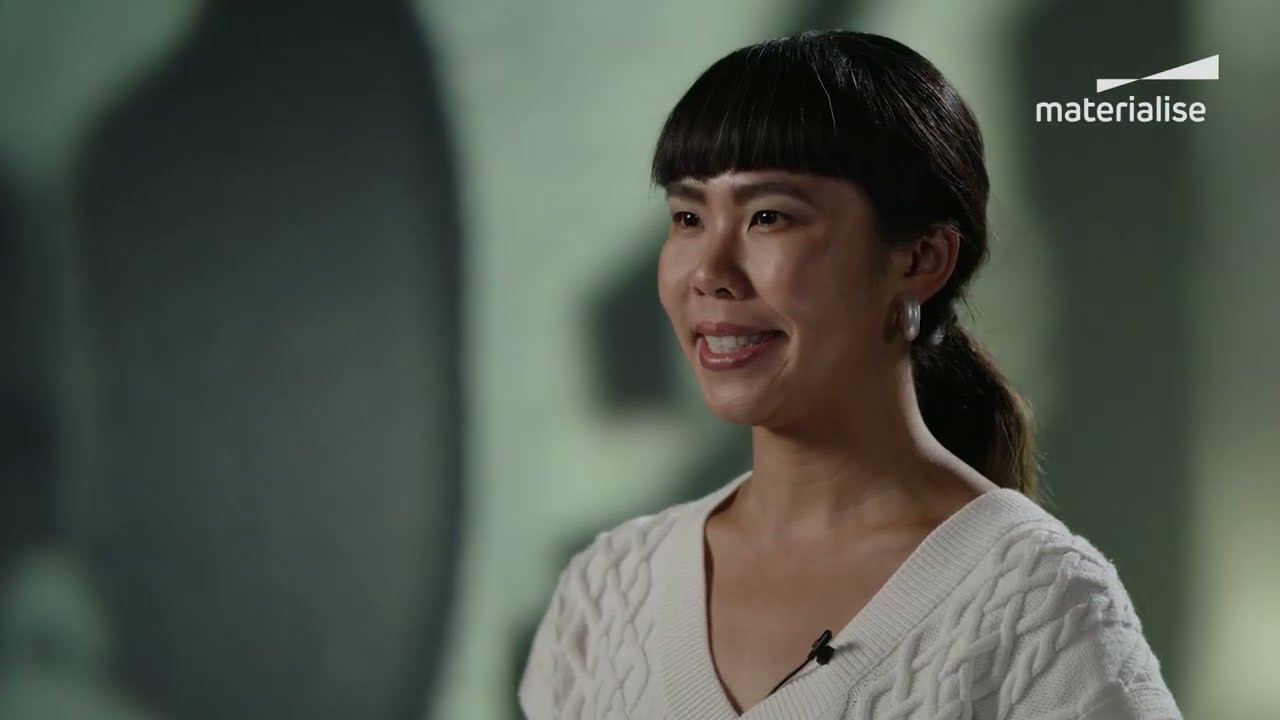
Selective Laser Sintering (SLS) is an additive manufacturing process that utilizes a high-power laser to selectively fuse powdered materials layer by layer, building three-dimensional objects with intricate geometries. The process begins with a powder bed, which is evenly distributed across a build platform. The laser, controlled by computer software, then traces a cross-sectional pattern on the powder bed, melting and fusing the particles along the path. After each layer is completed, the build platform descends, a thin layer of fresh powder is spread over the solidified layer, and the process repeats until the entire object is constructed.
One of the key differentiators of SLS from other 3D printing techniques is its ability to print in a wide range of materials, including plastics, metals, ceramics, and composites. This enables manufacturers to create parts with high strength, durability, and functionality. SLS also offers higher accuracy and resolution compared to other 3D printing methods, making it suitable for producing highly intricate and complex geometries. Additionally, the layering process in SLS allows for the creation of hollow structures, reducing the weight of the final product without compromising on its structural integrity.
How SLS Works
SLS follows a simple yet precise process to convert digital designs into physical objects. The following are the key steps involved in the SLS process:
1. Preparation of Powder Bed
The first step in the SLS process is preparing the powder bed. The powder bed acts as the base for the object being printed and needs to be evenly spread across the build platform. The type of material used for the powder bed depends on the desired properties of the final product.
2. Laser Scanning
Once the powder bed is prepared, a high-power laser is used to scan the surface of the powder bed. The laser is controlled by computer software that reads the digital design file and moves the laser in a specific pattern, tracing the cross-sectional layers of the object being printed.
3. Sintering Process
As the laser scans the powder bed, it heats and fuses the particles in the designated areas, bonding them together to create a solid layer. The heat from the laser raises the temperature of the powder particles above their melting point, causing them to fuse together and solidify.
4. Cooling and Solidification
After each layer is sintered, the build platform descends, and a fresh layer of powder is spread over the solidified layer. The laser then repeats the scanning and sintering process, building the object layer by layer. As each layer cools and solidifies, it fuses with the previous layer, creating a strong bond between the layers.
5. Post-Processing
Once the printing process is complete, the object needs to undergo post-processing steps. These steps include removing excess powder, cleaning the surface, and any necessary finishing processes such as polishing or painting.
History and Development of SLS
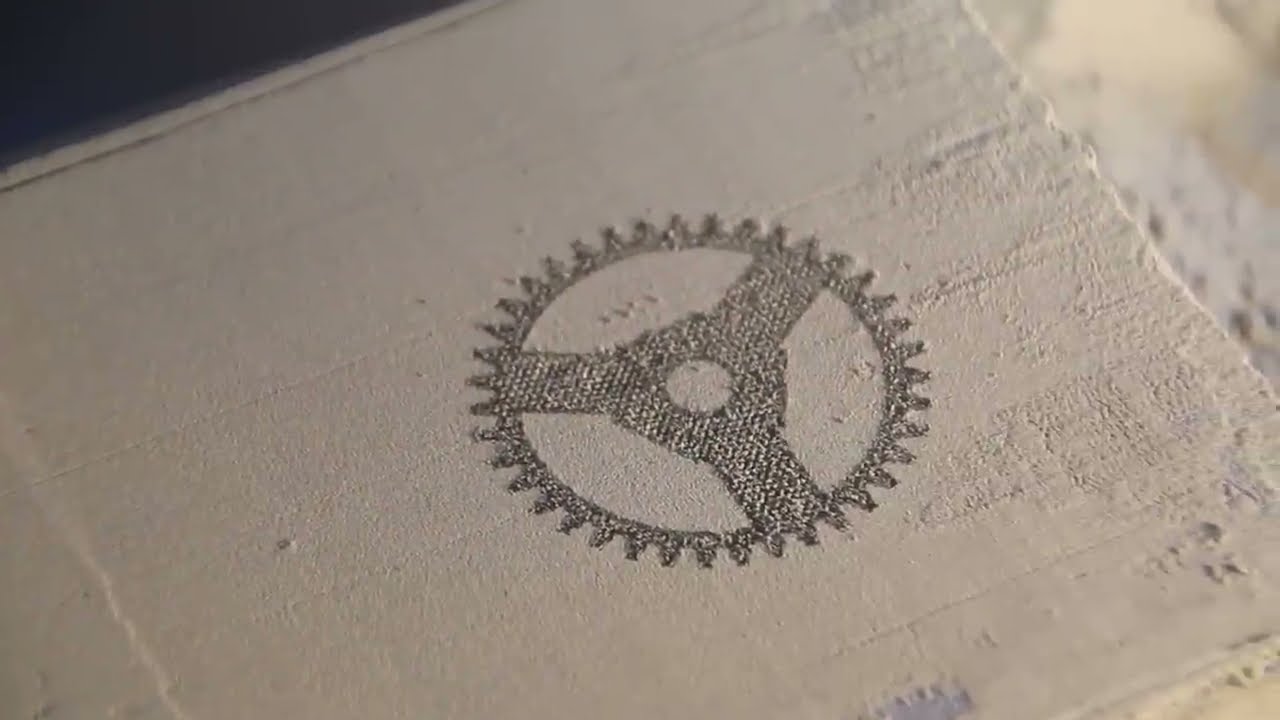
The concept of selective laser sintering was first introduced in the 1970s by Dr. Carl Deckard and Dr. Joe Beaman at the University of Texas at Austin. They developed the technology as part of their Ph.D. research in the field of additive manufacturing. The initial versions of SLS used carbon dioxide (CO2) lasers, which had limited power and accuracy, making them suitable only for producing simple objects.
However, with advancements in laser technology, especially the development of high-powered solid-state lasers, the capabilities of SLS were greatly enhanced. In the 1990s, the first commercial SLS machine was introduced by DTM Corporation, which is now a subsidiary of 3D Systems. This opened up new possibilities for using SLS in various industries and paved the way for further advancements in the technology.
Today, SLS has evolved tremendously, with a wide range of materials and machines available, each with its unique capabilities and applications. The development of new materials and the integration of SLS with other technologies, such as 3D scanning and generative design software, have further expanded its potential.
Advantages of SLS in Manufacturing
Selective Laser Sintering offers several advantages over traditional manufacturing methods, making it a preferred choice for many manufacturers. Some of these advantages include:
Cost-Effective Production
SLS is a cost-effective method of production, especially for small batch or customized parts. It eliminates the need for expensive molds or tooling, reducing the overall cost of production. Additionally, since SLS can print multiple objects at a time, it increases efficiency and reduces the cost per part.
Complex Geometries
SLS enables the creation of complex geometries that are impossible or extremely difficult to produce using traditional methods. This allows for more design freedom, resulting in innovative and functional products.
High Strength and Durability
One of the key advantages of SLS is its ability to print with a wide range of materials, including high-performance plastics and metals. This results in parts with high strength and durability, making them suitable for use in demanding applications.
Fast Production Time
SLS is a relatively fast process compared to traditional manufacturing methods. It eliminates the need for multiple steps such as tooling, machining, and assembly, reducing the overall production time. Additionally, since the laser can scan multiple layers simultaneously, it can produce complex parts in a shorter timeframe.
Applications of SLS in Various Industries
Selective Laser Sintering has found widespread application in various industries, each utilizing its unique capabilities to produce innovative products. Some of the key industries where SLS is being used include aerospace, automotive, healthcare, consumer products, and industrial manufacturing.
Aerospace Industry
The aerospace industry demands high-performance parts that can withstand extreme conditions while being lightweight. SLS is being used to produce components such as ducting, brackets, and housings for satellites, aircraft, and rockets. The ability to print complex geometries and use lightweight materials makes SLS an ideal choice for aerospace applications.
Automotive Industry
Automotive manufacturers have embraced SLS for producing functional prototypes and end-use parts. SLS is being used to produce parts such as engine covers, intake manifolds, and customized interiors. The use of SLS not only speeds up the prototyping process but also offers the flexibility to make design changes quickly.
Healthcare Industry
In the healthcare industry, SLS is gaining popularity for producing patient-specific medical devices, prosthetics, and surgical tools. SLS allows for the production of customized products that fit each patient’s unique anatomical structure, resulting in better treatment outcomes.
Consumer Products
SLS has opened up new possibilities for creating innovative consumer products with complex designs and functionalities. From customized phone cases to fashion accessories, SLS offers a cost-effective and efficient method for producing personalized products.
Industrial Manufacturing
SLS is being used in industrial manufacturing for producing tooling, jigs, fixtures, and other components. It offers a faster and more cost-effective alternative to traditional methods such as CNC machining or injection molding. Additionally, SLS also enables the production of one-off or low-volume parts, reducing inventory costs.
Case Studies of Successful Implementation of SLS
Selective Laser Sintering has been successfully implemented in numerous industries, resulting in significant improvements in efficiency, cost, and product innovation. Let us look at some case studies where SLS has played a crucial role in revolutionizing manufacturing processes.
BMW Group
The BMW Group is one of the leading automotive manufacturers in the world, known for its high-performance and luxury vehicles. In 2018, the company integrated SLS into its production process for the first time, using it to produce a water pump wheel for their DTM racing car. The use of SLS resulted in a weight reduction of 30%, improving the overall performance of the vehicle.
Procter & Gamble
Procter & Gamble (P&G) is a multinational consumer goods corporation famous for brands such as Pampers, Tide, and Gillette. In 2019, P&G began exploring the potential of 3D printing for their manufacturing processes. They used SLS to produce a customized nose clip for their Swiffer mop, eliminating the need for expensive molds and reducing the overall cost of production.
GE Aviation
GE Aviation, a subsidiary of General Electric, designs and manufactures aircraft engines. In 2014, they announced the successful testing of a 3D printed fuel nozzle using SLS. The use of SLS resulted in a weight reduction of 25% and improved aerodynamics, increasing the efficiency and performance of the engine.
Carbon
Carbon is a technology company known for its Digital Light Synthesis (DLS) 3D printing technology. However, to produce certain parts that require higher heat resistance and mechanical strength, they turned to SLS. By integrating SLS into their production process, they were able to print parts with complex geometries and high-performance materials, such as Nylon 12.
Future Trends and Innovations in SLS
The potential of Selective Laser Sintering is far from being exhausted. Research and development efforts are continuously pushing the boundaries of what is possible with SLS. Let us look at some of the future trends and innovations in SLS:
Multi-Material Printing
Currently, SLS can only print with one material at a time. However, researchers are working on developing multi-material SLS machines that can switch between different materials during the printing process. This will enable the creation of objects with multiple materials and properties, expanding the potential applications of SLS.
Integration with AI and Machine Learning
The integration of SLS with artificial intelligence (AI) and machine learning (ML) technologies is expected to further enhance its capabilities. This will enable the software to analyze and optimize designs, reducing the need for human intervention and improving the accuracy and speed of the printing process.
New Materials Development
New materials are continuously being developed to expand the range of materials available for SLS. Researchers are working on developing materials with improved properties, such as higher strength and flexibility, making them suitable for use in critical applications.
Large-Scale SLS Printing
Currently, the size of objects that can be produced using SLS is limited by the size of the build platform. However, researchers are exploring ways to overcome this limitation and enable large-scale SLS printing. This will open up new possibilities for using SLS in industries such as construction and architecture.
Conclusion
Selective Laser Sintering has emerged as a powerful and versatile technology, revolutionizing manufacturing processes in various industries. Its ability to produce complex geometries with high strength and precision has made it a game-changer in the world of additive manufacturing. As research and development efforts continue to enhance its capabilities, we can expect to see SLS playing an even more significant role in shaping the future of manufacturing. With its potential for cost-effective, fast, and customized production, SLS is undoubtedly here to stay and pave the way for innovative and functional products.