The manufacturing industry has undergone a significant transformation in recent years, with advancements in technology paving the way for more efficient and precise production processes. One such technology that is revolutionizing the manufacturing landscape is Laser Sintering, also known as Selective Laser Sintering (SLS). This additive manufacturing process uses a laser beam to selectively melt and fuse powdered material, layer by layer, to create complex three-dimensional objects. With its ability to produce high-performance parts with unparalleled precision and speed, Laser Sintering is quickly becoming a game-changer in the world of manufacturing.
Overview of Laser Sintering Technology
Laser Sintering technology was first developed in the 1980s by Dr. Carl Deckard and Dr. Joseph Beaman at the University of Texas at Austin. It was initially used for rapid prototyping, but over the years, it has evolved into a versatile and widely adopted method for producing end-use parts. The process involves the use of a laser to selectively fuse powdered material, typically plastic or metal, into solid layers. These layers are then built upon one another until the final object is created.
There are two main types of Laser Sintering – Selective Laser Sintering (SLS) and Direct Metal Laser Sintering (DMLS). While SLS is primarily used for plastic materials, DMLS is capable of sintering metals such as titanium, steel, and aluminum. Both methods use similar techniques, but the difference lies in the materials they can work with. In SLS, a CO2 laser is used, while DMLS employs a fiber laser for greater precision and control. Let’s take a closer look at how each of these processes works.
Selective Laser Sintering (SLS)
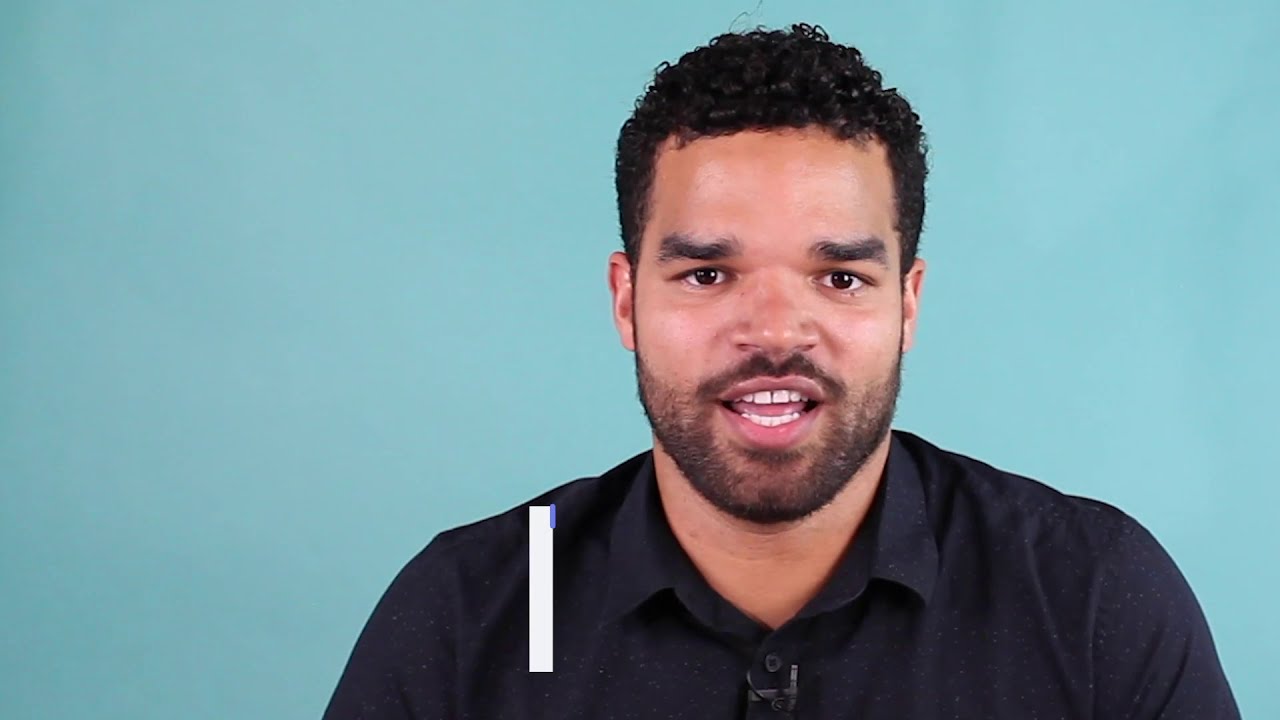
Selective Laser Sintering (SLS) starts with a thin layer of powdered material spread across a build platform. A CO2 laser is then used to scan the surface of the powder, selectively melting and fusing the material together according to a predefined pattern. Once a layer is completed, the build platform moves down slightly, and a new layer of powder is spread on top. The scanning and sintering process continues until the final part is complete. Any excess or unused powder acts as a support structure, eliminating the need for additional support materials. This allows for more intricate and complex designs without the risk of part distortion.
One of the main advantages of SLS is its ability to produce parts with a high level of accuracy and detail. As the laser only affects the areas that need to be fused, there is minimal wastage of material, resulting in cost savings for manufacturers. Additionally, SLS can work with a variety of materials, including thermoplastics, ceramics, and composites, making it a versatile choice for various applications.
Direct Metal Laser Sintering (DMLS)
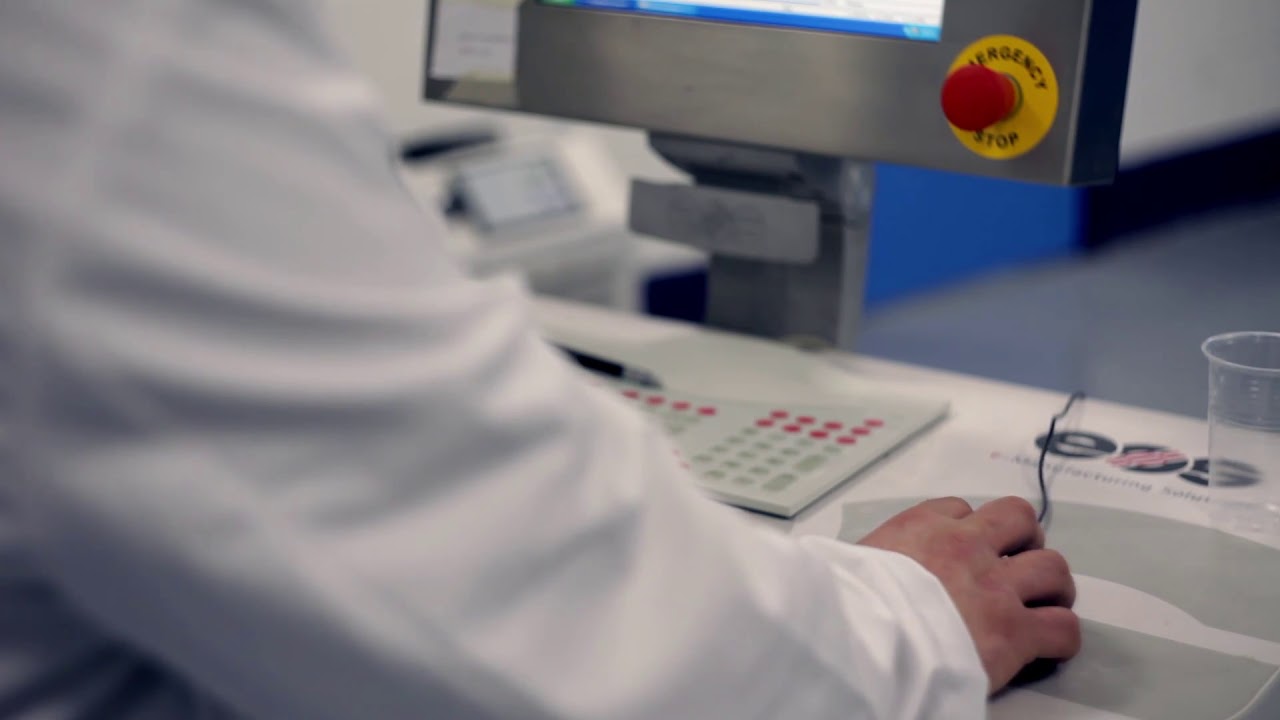
Direct Metal Laser Sintering (DMLS) follows a similar process to SLS, with some key differences. Instead of thermoplastics, DMLS uses metal powders as its base material, which are then melted and fused using a fiber laser. The laser is directed by a computer-aided design (CAD) file, allowing for precise layering and control. DMLS can produce parts with complex geometries and internal structures, which would be impossible to achieve through traditional manufacturing methods.
One of the key benefits of DMLS is its ability to produce strong, durable, and lightweight metal parts, suitable for use in aerospace, automotive, and medical industries. With its precision and repeatability, DMLS offers a cost-effective solution for producing small batch sizes of customized parts, reducing lead times and minimizing inventory costs.
Applications in Manufacturing
Laser Sintering has found widespread application across various industries, from aerospace and automotive to medical and consumer goods. Its ability to produce complex, functional parts with speed and precision has made it a go-to technology for many manufacturers. Let’s explore some of the common applications of Laser Sintering in manufacturing.
Aerospace
The aerospace industry requires highly specialized and lightweight components that can withstand extreme temperatures and pressures. Laser Sintering has emerged as an ideal method for producing these components, thanks to its ability to create intricate designs with high strength-to-weight ratios. From turbine blades to engine mounts, Laser Sintering is helping to push the boundaries of aerospace engineering.
Medical
Medical devices and implants often require customized designs to fit specific patient needs. Laser Sintering enables the production of patient-specific medical devices with high accuracy and reliability. It also allows for the creation of porous structures, which are essential for promoting bone growth and tissue integration. This makes Laser Sintering a game-changer in the medical field, offering faster production times and improved patient outcomes.
Automotive
With the automotive industry moving towards more electric and autonomous vehicles, there is an increased demand for lightweight, high-strength components. Laser Sintering is being used to produce parts such as air ducts, brackets, and housings, which are traditionally made through injection molding or CNC machining. Not only does this reduce material waste, but it also leads to cost savings and improved performance.
Consumer Goods
Laser Sintering is also making a significant impact in the consumer goods industry, where customization and personalization are becoming increasingly important. By using Laser Sintering, manufacturers can quickly produce one-off or limited-edition products without the need for expensive molds or tooling. This has opened up new opportunities for product designers and brands to innovate and create unique, high-quality products.
Benefits of Laser Sintering Technology
Laser Sintering offers several advantages over traditional manufacturing methods, which have contributed to its increasing popularity in the industry. Let’s take a look at some of the key benefits of this technology.
Design Flexibility
One of the biggest advantages of Laser Sintering is its design flexibility. Unlike traditional manufacturing methods, which require molds or tooling, Laser Sintering can produce parts with complex geometries and internal structures without any additional costs. This allows for more creative and innovative designs, resulting in better-performing products.
Cost Savings
Laser Sintering can also lead to significant cost savings for manufacturers. As it is an additive process, there is minimal material wastage, reducing the overall production costs. Additionally, without the need for expensive molds or tooling, manufacturers can save on upfront costs and produce small batch sizes without incurring additional expenses.
Faster Lead Times
With Laser Sintering, parts can be produced much faster compared to traditional methods. This is because the process requires no setup time and can run continuously, 24/7. This leads to shorter lead times, allowing manufacturers to bring new products to market quicker and stay ahead of the competition.
Better Quality Control
As Laser Sintering is a fully digital process, it offers greater control over part quality. Every layer is built according to a precise CAD file, ensuring consistency and accuracy. This also means that any changes or modifications to a design can be made easily, without the need for new tooling.
Case Studies of Successful Implementations
The success of Laser Sintering can be seen in its widespread adoption across various industries. Here are some examples of companies that have implemented Laser Sintering and reaped the benefits of this advanced technology.
General Electric (GE) Aviation
GE Aviation has been using Laser Sintering to produce fuel nozzles for its LEAP aircraft engines since 2015. These fuel nozzles are crucial components that determine the engine’s efficiency and durability. By switching from traditional casting methods to Laser Sintering, GE Aviation was able to reduce the weight of each nozzle by 25%, leading to significant fuel savings and improved performance.
Adidas
In 2017, sportswear giant Adidas launched its Futurecraft 4D shoe, which featured a midsole made using DMLS technology. Unlike traditional foam or rubber soles, the 3D-printed midsole allowed for more precise cushioning and support, tailored to an individual’s foot shape and movement. This innovative use of Laser Sintering has set a new standard in the sports footwear industry, with Adidas planning to produce millions of shoes using this technology in the future.
NASA
NASA has also been exploring the use of Laser Sintering for producing parts for its spacecraft and rovers. In 2016, they successfully tested a 3D-printed rocket engine injector that could withstand extremely high temperatures and pressures. The use of Laser Sintering has reduced production times and costs, allowing NASA to focus on developing cutting-edge technologies for space exploration.
Future Potential and Trends
The potential of Laser Sintering technology is still being explored, with ongoing research and development continuously pushing its capabilities. As the technology becomes more widespread and affordable, here are some of the trends and developments we can expect to see in the future.
Larger Build Volumes
One of the limitations of Laser Sintering currently is its build volume capacity. With advancements in laser technology and scanning techniques, manufacturers are working towards increasing the size of build platforms, allowing for the production of larger parts. This will open up new possibilities for industries such as automotive and construction.
Multi-Material Printing
Currently, Laser Sintering works with one material at a time, limiting its ability to create multi-material products. Researchers are working towards developing composite materials that can be sintered together, opening up new opportunities for the production of complex and functional parts.
Integration with Other Processes
As Laser Sintering becomes more widespread, we can expect to see it integrated with other manufacturing processes such as CNC machining and casting. This will allow manufacturers to combine the benefits of both traditional and additive manufacturing methods, resulting in more efficient and cost-effective production.
Conclusion
Laser Sintering technology is transforming the way we think about manufacturing. Its ability to produce complex and high-performance parts with precision and speed has opened up new opportunities for innovation and customization. With ongoing developments and advancements, Laser Sintering is well on its way to becoming an essential tool in the manufacturing landscape, shaping the future of design and production.