Introduction
In today’s fast-paced world, the demand for efficient and cost-effective manufacturing processes has never been greater. With the rise of 3D printing technology, industries are constantly looking for ways to improve their production methods. One such technology that has gained immense popularity in recent years is Selective Laser Sintering (SLS) 3D printing.
Selective Laser Sintering is a powder bed fusion process that uses a laser beam to selectively fuse powdered material into solid objects layer by layer. It offers a unique combination of material flexibility, design complexity, and cost-effectiveness, making it a highly sought-after technology in various industries. In this comprehensive guide, we will explore the principles, advantages, limitations, and potential applications of SLS 3D printing in detail.
Overview of Manufacturing
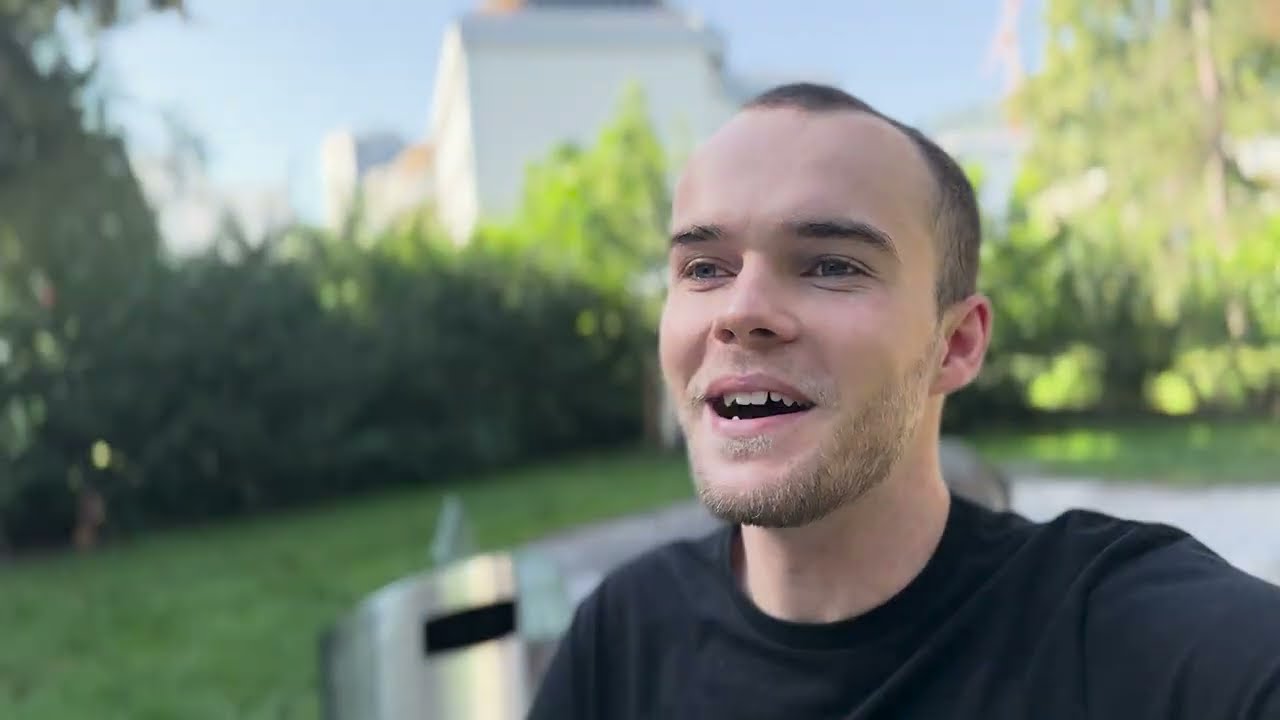
Before diving into the specifics of Selective Laser Sintering, let us take a quick look at the evolution of manufacturing over the years. The traditional method of manufacturing involves subtractive processes where raw materials are cut, drilled, or machined to create the desired shape. These processes are time-consuming, wasteful, and often limited in terms of design options.
With the advent of additive manufacturing, also known as 3D printing, a paradigm shift occurred in the manufacturing industry. Rather than removing material, additive manufacturing builds objects layer by layer, resulting in less waste and more complex designs. This technology has revolutionized the way products are made, offering endless possibilities for customization and innovation.
What is Selective Laser Sintering (SLS) 3D Printing?

Selective Laser Sintering, also known as Powder Bed Fusion, was first developed in the 1980s by Dr. Carl Deckard and Dr. Joseph Beaman at the University of Texas. It utilizes a high-powered laser to selectively fuse powdered materials, commonly polymers or metals, into solid objects.
The SLS process begins with a uniform layer of powdered material being spread over a build platform. A laser beam then scans the cross-sections of the object to be built, selectively fusing the powder particles together. The build platform then moves down by one layer, and a new layer of powder is spread over it. This process is repeated until the complete object is formed.
Applications of SLS 3D Printers in Manufacturing
Selective Laser Sintering is used in various industries for its unique capabilities, including rapid prototyping, tooling, and end-use production. Here are some of the most common applications of SLS 3D printing in manufacturing:
Rapid Prototyping
One of the primary advantages of SLS 3D printing is its ability to produce functional prototypes quickly and cost-effectively. Traditional prototyping methods can take weeks or even months to create a single prototype, making it difficult to meet tight deadlines. With SLS 3D printing, complex designs can be produced in a matter of hours, allowing engineers and designers to test and refine their ideas more efficiently.
Tooling
Tooling refers to the production of tools used in manufacturing processes, such as jigs, fixtures, and molds. These tools are often costly to produce using traditional methods and may require multiple iterations before achieving the desired design. SLS 3D printing offers a cost-effective and time-efficient solution for producing these tools, especially for low-volume production runs.
End-Use Production
Selective Laser Sintering has become increasingly popular for end-use production in industries such as aerospace, automotive, and medical. With advancements in materials, SLS 3D printers can now produce highly durable and functional parts that can withstand harsh environments and rigorous testing. This technology allows for on-demand manufacturing, reducing inventory costs and lead times significantly.
Advantages of SLS 3D Printing
SLS 3D printing offers a range of benefits over traditional manufacturing methods, making it a popular choice for industries worldwide. Some of the key advantages of SLS 3D printing include:
Material Flexibility
One of the most significant advantages of SLS 3D printing is its ability to work with a wide range of materials, including polymers, metals, and even ceramics. This versatility allows manufacturers to produce parts with specific material properties, such as strength, flexibility, or conductivity, depending on the intended application.
Design Complexity
Selective Laser Sintering also offers the advantage of creating highly complex designs that would be challenging or impossible to produce using traditional methods. The layer-by-layer building process allows for intricate internal structures that can improve the functionality and performance of the end product.
Cost-Effectiveness
While the initial cost of an SLS 3D printer may be higher than traditional machines, the cost per part is significantly lower. This is because SLS 3D printing does not require any tooling or fixturing, reducing the overall production costs. Moreover, the ability to produce multiple parts in a single print run saves time and labor costs, making SLS 3D printing a cost-effective solution for low-volume production.
Challenges and Limitations
Like all technologies, Selective Laser Sintering has some limitations and challenges that need to be considered before adopting it in the manufacturing process. These include:
Post-Processing Requirements
One of the main limitations of SLS 3D printing is the need for extensive post-processing. As the final product is still embedded in a bed of powder, it needs to be cleaned and finished manually. This can be a time-consuming and labor-intensive process, especially for complex or delicate parts.
Size Limitations
Due to the size of the build chamber, SLS 3D printers have restrictions on the size of parts they can produce. This limits the use of this technology for large-scale production, making it more suitable for smaller components.
Material Limitations
While SLS 3D printing offers a range of material options, some materials may not be suitable for this process due to their melting points or chemical properties. This limits the use of certain materials and may require manufacturers to explore other 3D printing technologies for specific applications.
Future Trends in SLS 3D Printing
The continuous advancements in technology are driving the growth of SLS 3D printing, with new developments and innovations emerging regularly. Some of the future trends in SLS 3D printing include:
Improved Materials
As the demand for end-use production using SLS 3D printing increases, there is a growing need for more durable and functional materials. Researchers are continuously exploring new materials and improving existing ones to meet the requirements of various industries.
Increased Speed and Precision
With improvements in laser technology, SLS 3D printers are becoming faster and more accurate, reducing print times and increasing productivity. This makes SLS 3D printing a more viable option for high-volume production in the future.
Integration with Other Technologies
To overcome the limitations of SLS 3D printing, manufacturers are looking at ways to integrate this technology with other processes such as CNC machining or injection molding. This will allow for more efficient post-processing and larger part sizes, making it a more versatile manufacturing solution.
Conclusion
Selective Laser Sintering has proven to be a game-changer in the world of manufacturing, providing a unique set of advantages that traditional methods cannot match. With its ability to produce complex designs, work with a variety of materials, and offer cost-effective solutions, SLS 3D printing is set to play a significant role in the future of manufacturing. As technology continues to evolve, we can expect to see even more advancements in SLS 3D printing, making it an essential tool for industries looking to stay ahead in a competitive market.